Dealing with energy overconsumption
With energy consumption at record highs, harnessing fertiliser from waste could prove an option in tackling energy deficiencies
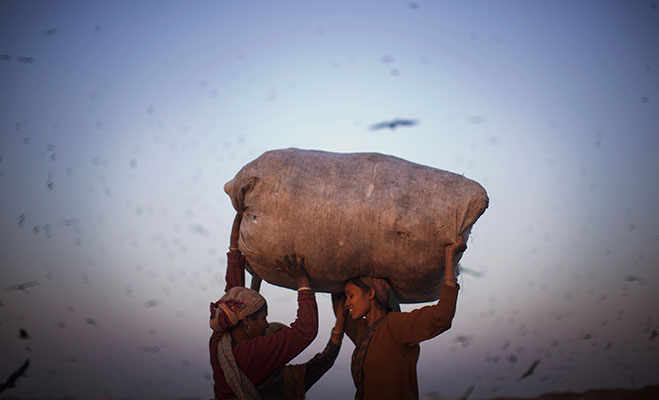
Between 1960 and 2011 the world’s population increased from three billion to seven billion people. By 2100 the world’s population is estimated to reach 10-16bn people. Even if municipal solid waste (MSW) per capita would stay constant, the total waste quantity will increase by 50 to 100 percent in the next century. In emerging economies such as China, India, Brazil and South Africa, wealth and income will increase steadily in the near future which then goes hand-in-hand with the MSW per capita (which develops in relation to income).
To compensate for the growth of MSW in emerging economies, global awareness and readiness to reduce MSW must rise drastically. Today and in the future the biggest portion of MSW will be landfilled. Harmful substances will be washed out and will penetrate into groundwater. Organic compounds of MSW will be transferred into methane and will then be released into the atmosphere uncontrolled. The negative environmental impact of methane is over 20 times more dangerous than carbon dioxide (CO2), and the environmental pollution caused by MSW will drastically rise in the next few years.
Considering that economic growth can cause higher amounts of commercial and industrial waste, it will become a real challenge to find an effective solution for proper waste treatment.
The growth of the world’s population will cause another problem. Even today it is proving extremely difficult to feed the world population. In the next few decades, usable agricultural areas will not increase. The only way to provide sufficient nutrition to an ever-growing population is to drastically increase the output of the agricultural area currently available.
A good solution would be to use more fertiliser. Urea is the most popular nitrogen-rich artificial fertiliser. In 2009 more than 130m tonnes of it had been produced, and usually the fertiliser is produced via natural gas. An increased demand for hydrocarbon and the limited resources of hydrocarbon materials have caused a constant price increase of urea. During the last three years, the world market price of urea has risen by 80 percent, reaching ¤350 per tonne.
Tackling the mentioned problems will prove to be a hugely challenging task. However, a potential methodology has emerged that may be able to offer sustainable waste treatment while simultaneously producing nitrogen-rich fertiliser from the subsequent waste.
Making the most of waste
Thermoselect high-temperature gasification is a thermal technology that allows ecological and complete thermal recycling of different kinds of waste such as: MSW, commercial solid waste, industrial solid waste, hazardous waste, automotive shredder residues (ASR), refuse derived fuel (RDF), sewage and industrial sludge.
Hydrogen-rich synthesis gas (syngas) is produced by compressing and degassing the waste in a degassing channel at temperatures of up to 500° C, followed by a thermal conversion of the organic compounds with pure oxygen in a high-temperature reactor at temperatures of up to 2000° C. Non-organic compounds are melted at temperatures between 1600°C and 2000°C. They result in recyclable, ecologically stable solid products (minerals and metal granulates). The oxygen used for the gasification of the organic compounds contained in the waste is produced on-site in a cryogenic air-separation unit. Air consists of about 80 percent nitrogen, which is not needed for the gasification process. Usually it is released into the atmosphere.
Beyond the high-temperature reactor, a quench is installed, where the synthesis gas is “shock-cooled”, avoiding the formation of toxic organic compounds like furans and dioxins. Most of the corrosive material is washed out from the synthesis gas into the quench water. Afterwards, the synthesis gas is neutralised in an alkaline scrubber, before entering a desulphurisation unit, where the sulfur compounds are oxidised to elementary sulfur. The devices for cleaning the synthesis gas depend on the use of the synthesis gas.
The synthesis gas consists of hydrogen, carbon monoxide, and carbon dioxide. The volume and composition of the synthesis gas depends on heating values and on the composition of the waste to be gasified. The cleaned synthesis gas for instance can be used to produce fertiliser without requiring limited, raw resources and without producing gaseous emissions like carbon dioxide. Seven Thermoselect plants are in commercial operation operating different kinds of waste.
Utilising the expenditure
The cooled and cleaned synthesis gas is initially compressed and converted by a process called ‘steam reforming’. This is performed in a reactor with a special catalyst and under defined parameters. Subsequently, carbon monoxide is then made from this synthesis gas, combined together with steam it is then transformed into hydrogen and carbon dioxide.
The next step in the process involves the hydrogen being separated in a state-of-the-art stripping device. The separated hydrogen and the nitrogen from the air separation unit are then used in a special reactor involving a specific catalyst for the ammonium synthesis. In the final step of the process, a urea synthesis takes place by using the resulting ammonia from the ammonia synthesis and carbon dioxide from the rest gas.
Depending on the characteristics of the input, a final production of about 600kg fertiliser per tonne of waste can be obtained. If the produced hydrogen as part of the synthesis gas creates a bottle neck, hydrogen can be supplemented to increase the ammonia production or ammonia can be purchased in order to increase the production of urea.
To produce fertiliser on an economically-viable basis, about 800,000 tonnes of waste per year are needed. The process described has numerous advantages to other methods. First of all, different kinds of waste are treated ecologically, with no gaseous emissions subsequently occurring. Coupled with that, the proper treatment of MSW becomes affordable even in emerging economies.
Furthermore, the fertiliser produced can be used in the nations where the most waste is generated. By using this method, the costs to produce fertiliser are much lower when compared to the average world market price. Finally, the fertiliser that is consequently produced is of an extremely high quality.